PRACTICUMS
During my time at Rose-Hulman, as an Engineering Design student, there are 4 quarters designated to a practicum. A practicum in this case is where I will work full-time as an intern at an engineering company, while simultaneously taking 4 credit hours of courses that relate back to what I'm doing at work. I did these during the summer before and after my junior year, as well as the fall and winter quarters of the same year.
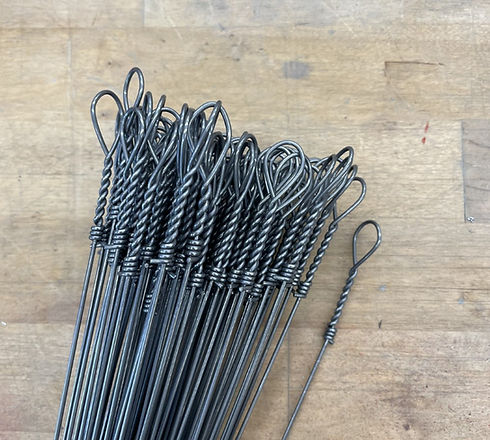

ROSE-HULMAN VENTURES
Rose-Hulman Ventures is an engineering consulting firm based in Terre Haute. I worked here in their Mechanical Engineering department and machine shop, working on two different projects during the summer of 2021, as well as the following Fall quarter. These two projects presented very different design challenges and kept me thinking constantly.
​
The first project depicted in the photos above was the wire-forming project. This one I can not go into great detail about as it had a nondisclosure attached to it, but after talking with my supervisor, this is what I am allowed to say (and show in the picture); I designed and built a semi-automated machine to help in the process of forming a wire and putting loops at either end. This was a great project that allowed me to be very creative on how I was able to design different parts of the machines, and I was able to work with the client quite frequently to make sure they were completely up-to-date on our progress, as well as making sure that we were both on the same page as to where the project was heading.
​
The second project I can talk a bit more specifically about. That one is a project we did for a company called Water for South Sudan. They are a company that helps get water and water pumps to rural areas in South Sudan and the surrounding areas in Africa. Our job was to find a way to make the water pumps that they were using more reliable and easier to maintain. Because the water pumps were degrading from use so quickly and often, a lot of them got abandoned due to the village being unable to service them themselves, and the inability to contact those who could come out and fix them. This results in fewer people having access to clean drinkable water, so we worked with them to find several ways on improving the longevity of their pumps. For us, this meant performing lots of stress tests along with redesigning a number of different parts.

CATALYST PRODUCT DEVELOPMENT GROUP
Catalyst Product Development Group is a product design firm based out of Indianapolis, Indiana. One thing that makes Catalyst stick out is the injection molding and tooling shop they have in the same building. During my time here, I worked in the Product Development Department half time, and in the shop half time. Working in these two areas gave me a wide range of different experiences. I was able to both work directly with clients to design and develop their products, as well as learn a bit about the intricacies of injection molding while working in the shop.
​
While I was in the product development department, I was mainly focused on one client, while helping out with odds and ends on other clients' projects as well. The main project I worked on was a new medical device that I worked with medical personnel to develop. This device would be used in the ER room at their hospital and sold to other hospitals once taken to market. This project was a fun one for me to work on as I have found that I love working directly with my clients. Also, it gave me a great insight into doing research on what types of materials different products should be made out of. For this product, it had to be a product that could easily be sterilized through hospital-grade sterilization methods, strong enough to be hit and not get damaged, as well as flexible enough to make the geometry and functionality of the part work reliably. Finding the materials that worked, in this case, brought me on a journey that taught me a lot about material sciences.
​
With this project, I also learned a bit about how to render different designs. Specifically, I was taught how to bring SolidWorks files into KeyShot to then make realistic and nice-looking renders to show to the client and to use for advertising. I was only taught the basics with the time I had but with a little bit of help from the team, I was able to put together some presentations using this method to present the final product to the client. I am definitely interested in looking into this further later on in my career.
​
The second half of my work week was spent in the injection molding shop. Here, I learned how to operate the injection molding machines and a bit about different thermoplastic material properties. One of the projects I was around for was the testing of a new 3d printer that Catalyst had purchased. Specifically, this printer was able to print with ceramics, so we were trying to see how feasible it would be to 3d print tooling for low production prototyping for their injection molding machines. To test this, they made a mold for the company logo, this test can be seen in the image for this section. I had a lot of fun working in the injection molding shop and connecting the dots of design principles that I've been taught in class to real these life processes and products.